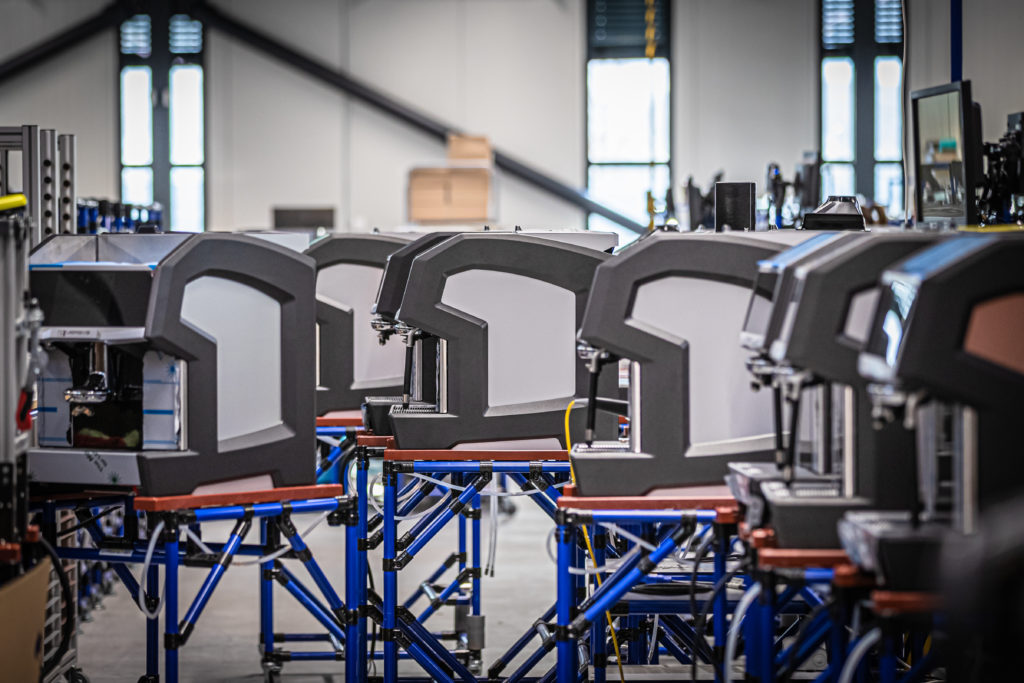
Photo: Eversys
Swiss coffee machine manufacturer Eversys moves to its new factory in Sierre, which is believed to better serve the company’s international business and offer a great lift of its brand image.
Boasting a volume of nearly 44,000m3, the site construction is 115m long by 50m wide, split into two floors. “Our presence in Daval will allow us to double production capacity, reaching 10,000 coffee machines a year,” explained Jean-Paul In-Albon, founder of Eversys, “We’ve even kept a reserve of land for further development.”
In the past months, Eversys has been making its transition smoothly yet efficiently into its new home factory. The first ever machine was produced at the new site on Jan.17.
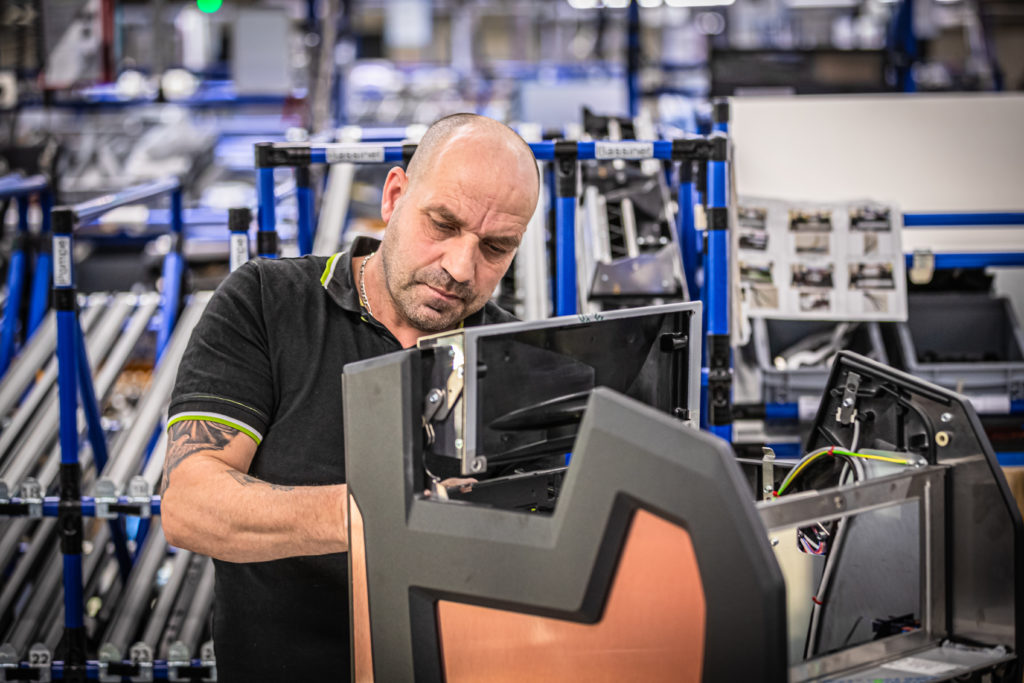
Photo: Eversys
Technology Empowers…
The big change behind the company’s move also lies in the introduction of its new ERP solution SAP. Together with key users, the project team from De Longhi, E-Service and Eversys worked for the implementation of this SAP solution, which is expected to help integrate all departments and support Eversys’ growth.
Eversys CEO Martin Strehl shared, “Moving into our brand-new factory and in parallel introducing our new ERP solution SAP feels like moving from the 2nd National League to the Champions League in one go. We are all very excited and proud to make this big step, which will allow us to continue our ambitious growth plans as well as to further increase our efficiency and quality.”
With all efforts, the SAP solution has been now running since Jan.6. It also introduces an online ordering system as the web platform offers a wide range of possibilities, for example, customer-controlled machine configuration, spare parts ordering and RMA (return merchandise authorisation).
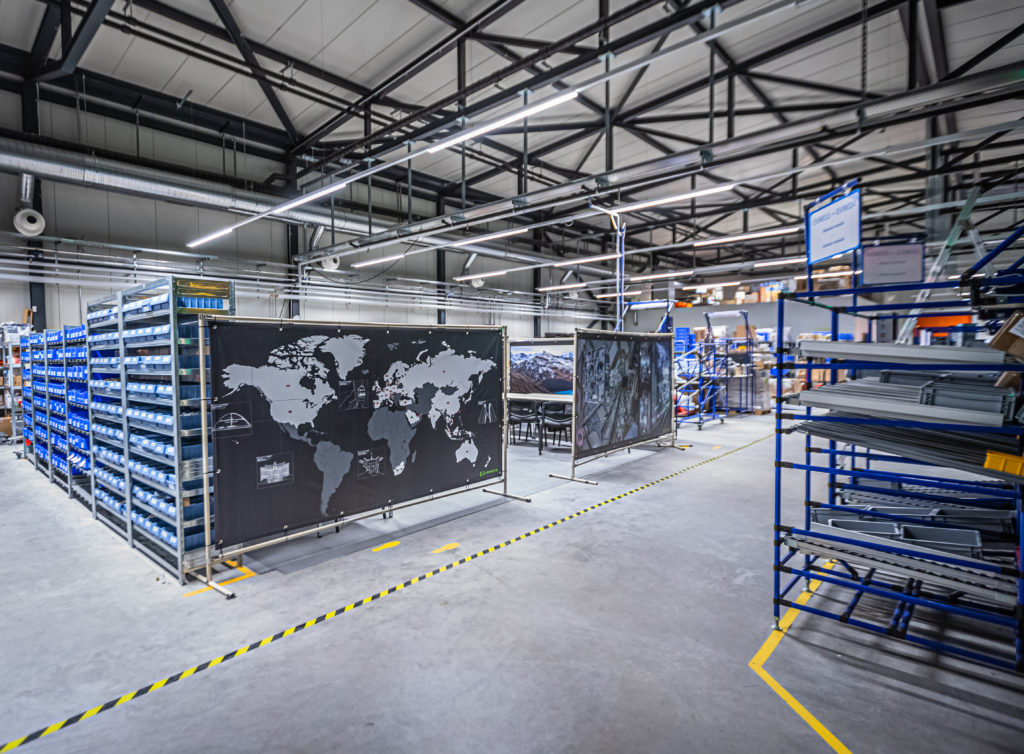
Photo: Eversys
The system was tested and retested by selected key users before validation as well. Andrea Romanin, operations director at Eversys, said, “Together with the Italian De Longhi team and E-service, all departments have defined best practices together to improve Eversys operations and carry out all the necessary processes.”
As a step forward in terms of efficiency and time saving, SAP allows orders to be executed directly in the system by customers, which helps prevent possible errors from entering data.

Photo: Eversys
Meanwhile, the production and logistics evolve greatly due to the introduction of SAP. Production goes digital as everything can be modified online. The store is organized like a supermarket, for example, with all the parts and products necessary for production. The parts are transferred in the aisles with an electric train and scanners are used for each transfer. As the efficiency of such transfers improves, the production process is now managed by 45 stations across assembly lines known as the e’line and the c’line, which was set up by Jan. 6. “Having a fully digitalized procedure allows better inventory management in real time, simplifies declarations and prevents errors. These processes also improve product traceability since each module is scanned before being inserted into a coffee machine”, said Vincent Berthod, production manager.
This digitalization also benefits the purchasing department for it is a time saver for them to optimize deliveries and know exactly what parts in need and when.
On the other hand, Eversys’ customers can get a clear ‘map’ of their orders with visibility of delivery times, how long the production time, and etc.
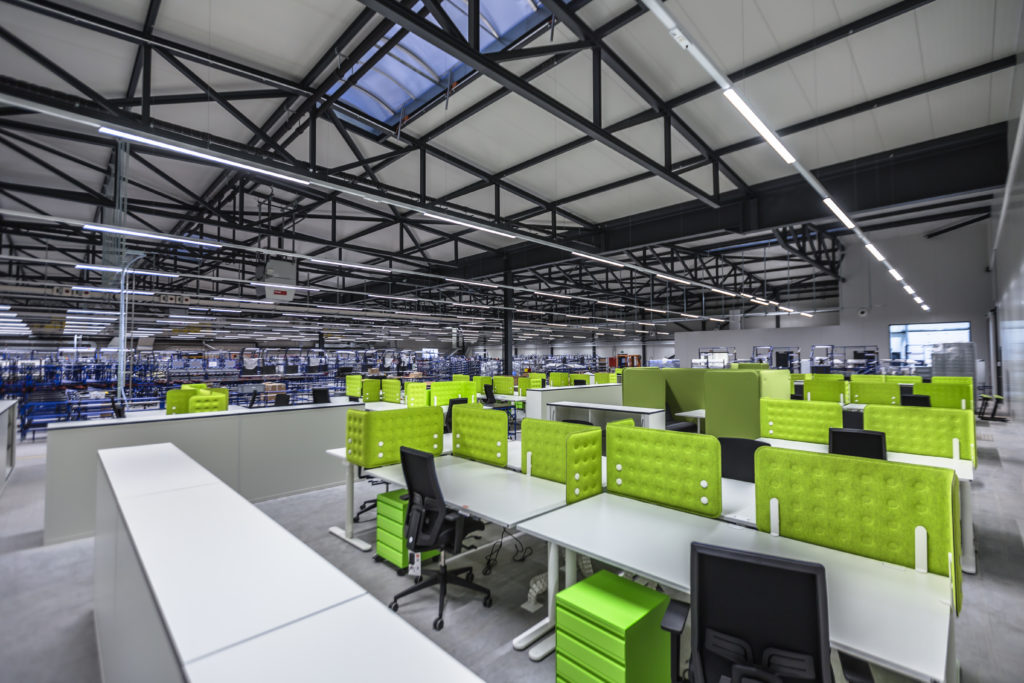
Photo: Eversys
An Insight from Insiders
Since Jan.6, the customer services, purchasing, finance, quality, production, logistics and IT teams of Eversys have been brought together in the new Sierre building. We asked them three key questions a few days after their move in early January.
Fabiola Rouiller, Assembly-line Worker, production department
Neslo Cruz, Customer Service Manager, logistics department
Corinne Genoud, Commercial Customer Support, customer service department
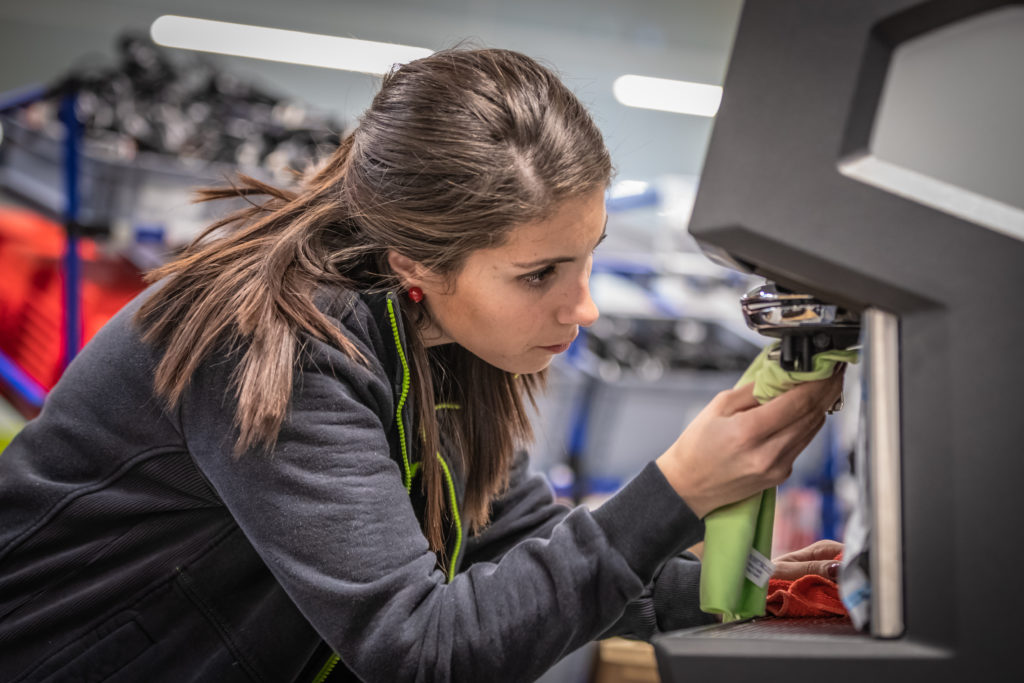
Photo: Eversys
- How was the move?
FR: The move went very well, especially since I was on holiday between the departure from Vétroz and the arrival in Sierre. Today, I discovered the work carried out by my colleagues: they took out everything that we had put in the boxes and rebuilt all the production stations in the new hall.
NC: The move went well. We had to move a lot of equipment and prepare countless things; it involved a fair amount of organization and a lot of planning. It was necessary to make the transition between Vétroz, Ardon and Sierre while introducing the new SAP for customer service. It has been an interesting challenge!
CG: The move went very well. We left Ardon on Friday, 3 January at 2:30pm and at 3:30pm we were ready to work. Everyone took their computer and their car. Because everything is computerized, there were not a lot of boxes. We arrived with a truck and installed the equipment. It was quick and simple.
- What do you think of the new installations?
FR: I find the building and the facilities to be very nice. The move brings with it a lot of changes. The commute is not long for me, I just have to remember to set off in the direction of Sierre in the morning. Otherwise, I look forward to starting production.
NC: There’s nothing to say. All the means are there to move forward better, faster, manage handling… it’s very comprehensive. From a logistical point of view, Ardon and Vétroz were no longer suited to our work. Here, we have greater amounts of space.
CG: On Friday we were in an open space with no partitions; it was different from how it is now. With the large partition on the north side, it is no longer cold, and we feel comfortable. I really like the new dynamic of this workplace, being all under one roof brings us together. Our improvised office is only provisional because in April we are going to move to the administrative area.
- What advantages does it bring to your work?
FR: My daily work hasn’t really changed. We are still three colleagues on the production line; I can tell you more as soon as we begin production. There, I set in place, clean and put the finishing touches to everything.
NC: The fact that everyone is there helps with coordination. From an internal point of view, we will be much more efficient, and information will circulate quickly and more easily. We will be able to settle things in person. It’s really positive.
CG: Better interdepartmental communication, I would say, thanks to this new proximity with customer service. Moreover, with SAP we are still in the testing and implementation stages and having everything in one place is practical. During the first months, we have to adapt and develop good habits.
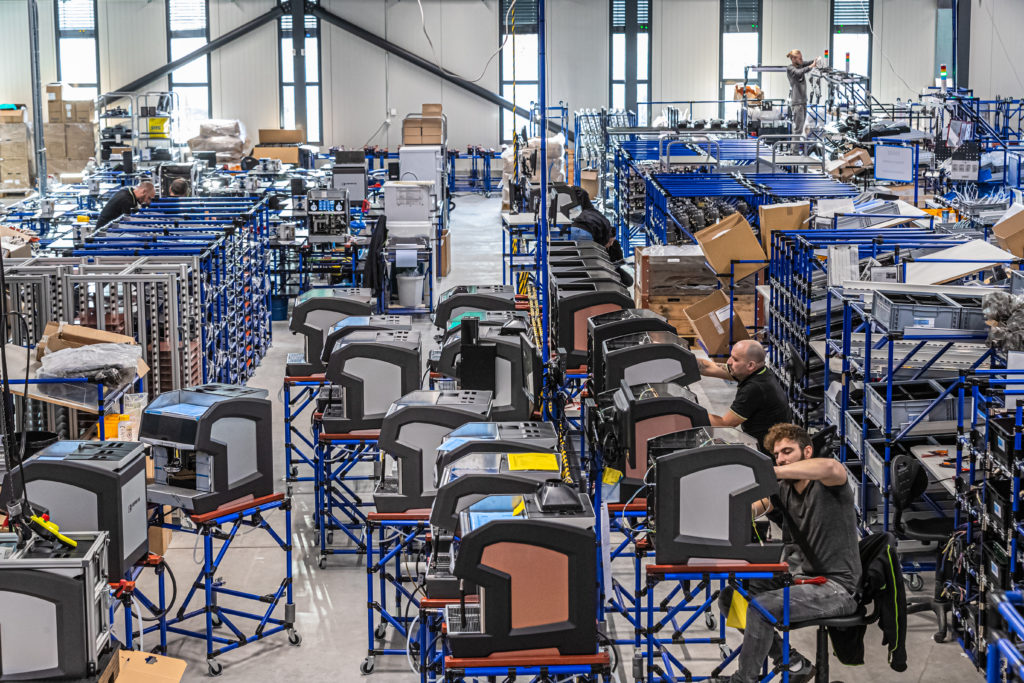
Photo: Eversys
NO COMMENT